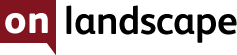

The Inside Track from Jon Cuff

Jon Cuff
Jon has been in the photographic industry since his teenage years where he started work at Robert White Photographic in Dorset after he left college. After almost 15 years of service; working with some of the most interesting brands and formats; from large format film to digital backs (and almost everything in between) it was time for a change. Luckily a position at LEE Filters opened up a couple of years ago. Jon works with a small team and between them they cover LEE world-wide sales and technical support; outside of the US, for the photographic, film & TV, theatrical and architectural markets.

Tim Parkin
Amateur Photographer who plays with big cameras and film when in between digital photographs.
On a recent visit to On Landscape headquarters we asked Jon Cuff whether he would be able to answer a few questions about the process of creating the filters and a few questions from our readers as well. Jon graciously agreed and also took a few photographs of the operation for us.
When people see a Lee filter for the first time, there is a perception that you must just buy in a sheet of clear plastic, dye one end and then chop them to size and wonder why they are so expensive. Could you let us know just how the filters are made and why the processes are so demanding? i.e. plastic type, optical purity, how to get parallel/smooth, how to get neutral dyes, how to get the right gradation.
Firstly, it is important to note that our resin filters are made by hand in Andover, Hampshire. It is here we convert a selection of raw materials into the filters many of our customers know and love. The resin used in our filters is a formulation known as CR39 (which has the highest abrasion/scratch resistance of any uncoated optical plastic). This is similar to that used in the manufacture of spectacle lenses, but it is not the same. We buy the constituent parts of a CR39 resin, and our team of chemists formulate it to our own specifications and tolerances in house. This gives us ultimate control over the quality of the resin; plus the mixing conditions we use gives a superb optical clarity that we could not achieve by simply buying in sheets.
Once we have the correct formulation we cast the resin sheets in a ‘mold’ of two perfectly flat pieces of float glass. The thickness of the filter is controlled by a specifically made filament system. The combination of the glass and the filament allows us to achieve perfect flatness as well as a parallel sheet. These ‘molds’ then go into a highly programmable oven which cures the resin for 24 – 48 hours.
Once removed from the ovens the filters are tested for optical clarity, flatness and hardness. If they pass all of these requirements, they are then sent on to our dedicated resin dying team.
All of the dyes we use are, again, supplied to us in a raw form and are formulated from a number of individually coloured dyes on site. This allows for very fine control in maintaining the accuracy of our colours as we can adjust the final dye depending on any variables that we may encounter.
All resin filters are hand dyed in tanks heated to a specific temperature. The heat will enable the dye to migrate into the surface layers of the resin. The density of the filter is not only affected by the dye itself but also the duration in the dye tank.
Graduated filters are partially dipped into the dye and agitated depending on the type of graduation we are producing. This is a very time-consuming process which can vary from filter to filter; for example, a 1.2 (4stop) ND takes longer than a 0.6 (2 stop) ND.
All filters are then given visual checks that are also confirmed by spectrophotometers to ensure they meet specification.
The filters are then cut to the correct size, sent through a rigorous quality control and then packed for worldwide dispatch.
During the whole process, each filter will undergo at least 12 separate quality checks, and of course, can be rejected and discarded at any point. We have quite a high waste figure, but an incredibly low returns rate, and that’s how it should be.
Recently Lee has introduced two new gradations, the very hard and medium ones, to make a total of four different gradations. Where did the demand for these come from and are they proving popular?
The new graduations have been received very well indeed. For those who don’t know; we have added medium and very hard to the 100mm and SW150 systems and a medium to the Sev5n. In truth, we have been making these graduations in one form or another for our professional photographers for some time now. There were a few reasons to offer them as a general release.
"Which Graduation?"
We're currently doing some research and testing to work out which graduation is best for a particular lens/camera system but in short we're pretty sure it depends on three things 1) Focal length - longer needs harder 2) Distance of filter from nodal point of lens - farther needs harder 3) Aperture - larger needs harder (e.g. f/1.4 blurs the edge of a hard grad)Firstly, we wanted to give the photographer as much creative control as possible. Secondly, with the ever increasing popularity of APS-C / M4/3 mirrorless systems we wanted to give a harder graduation range that would be better suited to their equipment needs. Lastly, focal length has a direct effect on the usefulness of a grad with longer focal lengths requiring a much harder edge.
The very dense neutral density filters have proved very popular and are glass based rather than plastic. How are these manufactured and how hard was it to get a result that has minimal colour casts?
It is worth noting that the vast majority of our range is still made from resin. However, sometimes it is necessary to produce a filter in glass. In the case of the Stopper filters; glass was an essential part of their design. Glass has to be used in order to block the infrared colour cast associated with long exposures. These filters are made in a deep dye process where the dye is mixed into the molten glass rather than a surface-coated treatment. This not only locks in the dye, making it permanent, but it also enables us to achieve the high densities we require. The essential part of the process is to get the dye mix correct at the point of casting. Once cast, the colour cannot be changed. After the casting process is complete, the glass is cut into sizes and then highly polished to a finished surface.
A couple of manufacturers make glass graduated filters (albeit only in soft gradation and at enormous expense). Have you considered producing your graduated filters in glass?
We never discount anything, but we will only produce out of glass if we are confident it is better than we currently make. At this time we plan to stick with resin. There are a number of reasons why we continue to use resin for the majority of our products, but the main one is the ability to control our graduation types. By using resin, we can dip dye the filter in tanks and tightly control the differences between the four graduation types. Glass grads are made in a very different process where a vaporised metal is effectively sprayed onto the surface of a glass substrate. The clear part of the filter is shielded off, thereby giving you a graduated filter. This process often leads to big variations in the graduation lines, often leaning more towards a softer edge. Using glass also adds the complication of reflectiveness. By adhering metal to a glass surface, you are effectively making a mirror. It is, therefore, necessary to add all types of anti-reflective multi-coatings to combat this. We do not experience such an issue with the resin filters we make.
Colour correction filters used to be very popular for film use. Are you seeing demand for these filters again now that film is becoming more popular?
Digital photography has meant that we do not sell as many colour correction filters as we use to, but the demand has never totally gone away with even a number of digital photographers preferring to use some of the weaker variants. We have seen more and more film based photographers get in contact with us, especially if they are planning long exposures using a Stopper; combating the blue colour cast with one of our amber filters.
Strongly coloured filters for black and white film photography can create some dramatic looks or just give increased contrast etc.
What are the most popular of these?
Black and white landscapes are ever popular and I am pleased to say that many still use traditional black and white film. We make a select range of black and white filters, each with their own benefits. Yellow absorbs blue in images, which has a great effect on darkening skies and foliage. Yellow-green is great for lightening foliage and grass and darkens reds. Reds and oranges are ideal for adding drama to an image with an increased contrast, absorbing blues/greens with the effect of the red filter being very strong. We even have some digital photographers use these filters effectively too (Tim: Be wary though, very dense red or blue filters can have a big effect on resolution)
Gel filters are considerably cheaper than resin ones, what are the disadvantages of using these?
To clarify, we make a couple of gel filters. One is our range of lighting gel. These are sold in sheets and rolls and are for lighting control only. Sadly they do not have the optical quality to be used in front of a lens.
The other type of gel is a select range of polyester camera filters. These super thin gels offer incredible optical quality due to the fact that they are so thin and therefore have a very low refractive index. However, they need to be mounted in a frame to be used in a holder. Their thin nature makes them more delicate than resin, and they can damage easily. They are an excellent option when a temporary solution is needed. It is worth noting that we cannot offer graduated filters or strong ND’s in polyester gel form.
In terms of product development, have a look in the crystal ball and tell us what you see in the potential Lee filters pipeline.
We are lucky to have a very active R&D team. A great deal of work is put into investigating new technologies, applications and ideas. Sadly R&D are a secretive bunch so sadly no juicy bits today I am afraid. However, we do endeavour to view our product line in a wider scope and are already seeing photographers and film makers use our filters in increasingly creative and different ways. We take a great deal of inspiration from this and look to develop products that not only offer filtration but support the photographer too.
Questions from Readers
We like the new dayglo 75mm adapter caps, will you be doing similar ones for the 100mm system? Can you redesign the 100mm caps to make them fit better, protect the lens better and more easily removable?
The new Sev5n caps have been very well received. At the moment we do not have plans to replace the 100mm system cap, but you never know. The 100mm system caps have to be of a different design because of the more complicated shape of the 100mm adaptor rings, and we originally made them white so that you can also take a fairly good white balance reading through them.
Can you make adapters that repeat the lens thread so I can use my own lens caps?
This is something we used to have but changed some time ago when we widened the design of the standard rings to give more angle of view. The far more popular wide angle style rings are made to be incredibly thin and by design have no area for a repeat thread.
Lots of people are asking about a reverse grad - can you tell us what the problems with this are?
We do get asked for reverse ND grad filters, and it is actually something we are looking into. However, we believe we have a very good reason why we have not offered them in the past. Most customers use such a filter for sun below the horizon shots, seascape sunsets, etc. and want a very hard grad line at the horizon with a short graduated area to darken the sun. Reverse ND grads as they are currently available do offer a hard horizon line edge, but the blend to a fade can often be too wide, or the lens itself is not seeing a wide enough expansion of sky to see the faded area. In many instances, an ND stripe works well.
Before you ask, sadly we do not currently offer a ND stripe, but there is an option by using two ND grads together. If you insert one of the grads upside down you can overlap the filters; where they cross you get a ND stripe.
This is not only adjustable to suit your scene and or focal length of lens but you can vary the effect massively by using different strengths and graduation types. This gives the photographer a lot of control. Using this technique does mean that you have to allow for the second ND grad affecting your foreground exposure but once you understand the technique it is very simple. That being said, if we can produce a reverse ND grad that we feel offers the photographers what they want, we will do all we can to do that.
What do you recommend to clean the filters? Will using natural soap cause any problems?
We do have a cleaning solution in our range that works well, if you have other filter/lens cleaners they should be ok too as long as they are not aggressive in their cleaning action. If you shoot near the sea and find that at the end of a session you have a lot of salt on the filter, we would recommend washing this off first. Luke warm (NOT HOT) water is ideal. This will dissolve the salt away. Once dry you can polish with our cleaning solution and a cloth.
Filters eventually change colour. How long should a Lee filter last and stay within spec? Can you do trade in discounts on updating filters that have gone out of spec?
As the dye in the resin filters is a surface coating, it can fade after use and time. With good storage, you can expect to get 7-10 years of use out of them. Sadly we do not do any trade in schemes to replace these filters but as all of our filters are dated, if a problem occurs before this time, a customer can contact us directly, and we can sort it out.
Will you be making an adapter or system for the Canon 11-24mm fisheye?
We currently have an adaptor for the SW150 system that works with the Canon 11-24mm lens. It is worth noting however that vignetting does occur at 11mm. You can, however, use the holder fitted with two slots at 13.5mm and one slot at 12.5mm. These figures are when the holder is being used relatively straight. If you angle the holder, then the vignetting issue is much greater, and you have to sacrifice more focal length. The only way around this would be to make an even larger filters system with dramatically wider filters. At the moment this is not something we are planning to do.
Is there any way Lee can make the grad transition zones more uniform at each given style i.e., soft, medium, hard. I virtually always use multiple grads to arrive at my requirement but none of the transition at the same rate.
As our filters are hand-made there is a tolerance to each of the graduations. However, there are very distinctive differences between them. Due to the different depths of each graduation transition there can be a variance from one type to another, especially if you are using a soft filter with a harder one at the same time. Since we changed to the 4 variations of gradation, we have had to tighten our tolerances for manufacture even further. But because the filters are made by hand there will always be some variation from filter to filter, but you will find that LEE filters made in the last 2 years or so will have much less variance in the transition zone than filters from a few years back.
Do you still see a place for graduated filters as digital cameras have more and more dynamic range?
Dynamic range has indeed become much better in recent years, but we find that there is still a need for a graduated filter. Even the most modern cameras with impressive dynamic ranges often need a two stop grad to give them a balanced image. We are seeing that customers need less ND strength to balance their image than they use to, but there is still some way to go before we wave goodbye to graduated filters.
A big thank you to Jon for his answers to our questions. We'll have our research into how to choose your graduated filters in a future issue - if anybody would like to help who has a range of lenses and a Lee filter holder, please get in touch!
On Landscape Meeting of Minds Conference
Jon Cuff will be on the Linhof Studio stand at the conference this November, so if you have any questions for Jon, please do visit him on the stand.
Lee Filters DSLR Starter Kit Offer from Linhof Studio
Buy the Lee Filters DSLR Starter Kit and get the wide angle adapter free. This retails £45.48 inc VAT.
The starter kit retails at £245 inc VAT and includes:
- 1X Lee Filter Holder (already assembled)
- 1X 0.6ND Hard Grad 2 stops 100x 150mm
- 1x Pro Glass 0.6 ND 2 stops 100x 100mm
- 1x Cleaning Cloth
- 1x Tri Pouch